De quoi et comment sont faites les briques ?
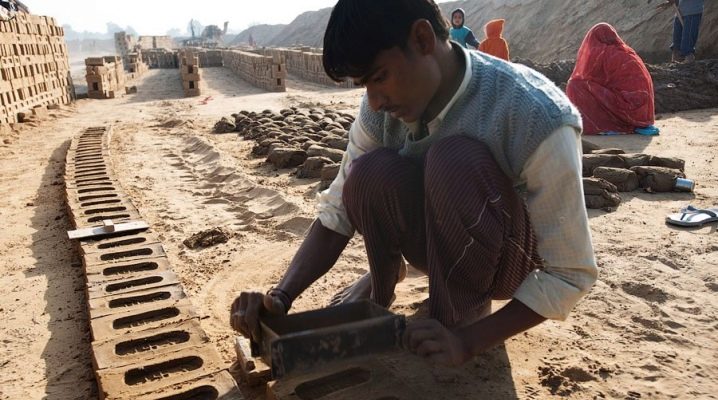
De nombreux avantages font de la brique l'un des matériaux de construction les plus recherchés. En plus des tailles standard et des formes simples, cette pierre artificielle possède résistance, durabilité et beauté, c'est pourquoi elle est utilisée depuis très longtemps et presque partout.
Il convient également de noter les technologies avec lesquelles la brique est fabriquée - en tant qu'ensemble de processus permettant d'obtenir un matériau avec toutes les caractéristiques dont le client a besoin.
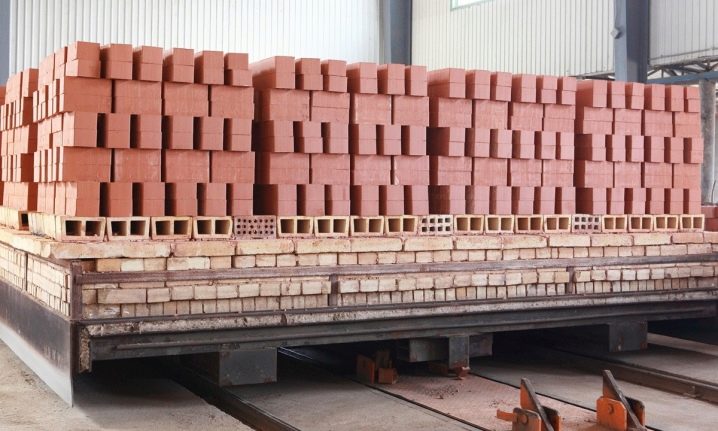
Composition selon le type
Parmi tous les types de briques, deux sont les plus populaires - la céramique et le silicate, également appelées respectivement rouge et blanche.
Ils diffèrent par les caractéristiques suivantes.
- Le composant principal des briques céramiques cuites est l'argile. Un tel matériau a un aspect esthétique, amortit le bruit et stocke parfaitement la chaleur dans la pièce.
- La composition des briques de silicate, fabriquées sous l'influence de la haute pression et de la vapeur, prévoit la présence de sable et de chaux. Le respect de la technologie vous permet d'obtenir des produits durables et peu coûteux pouvant résister aux changements de température et d'humidité.
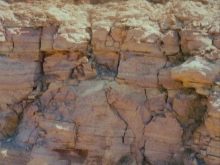
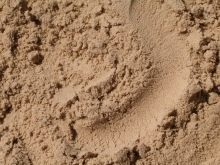
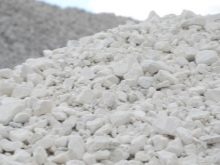
Il est également nécessaire de mettre en évidence les briques réfractaires en chamotte avec ajout de coke ou de graphite - des composants qui augmentent considérablement sa résistance.
Une autre variété topique est confrontée, dont la production implique l'utilisation de ciment, de calcaire et d'un ingrédient pigmentaire. Une telle brique, fabriquée par la technologie de pressage, a non seulement un aspect esthétique, mais également une durée de vie impressionnante.
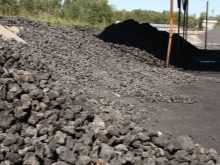
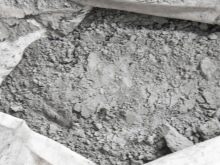
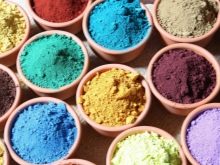
Compte tenu de la plus grande importance des variétés rouges et blanches, elles devraient être examinées plus en détail - ce qui sera fait ensuite.
Céramique
L'ingrédient principal de ce type de brique est l'argile ordinaire. C'est une masse minérale qui :
- devient plastique lorsqu'on y ajoute de l'eau;
- conserve sa forme pendant le séchage;
- durcit à la suite de la cuisson, acquérant une résistance comparable à celle de la pierre naturelle.
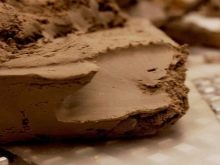
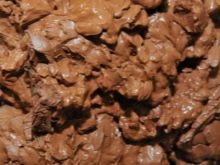
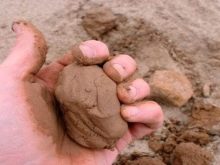
L'origine de l'argile utilisée mérite une attention particulière. Selon la profondeur, il peut avoir des propriétés différentes - à la fois adaptées à la production de briques et ne répondant pas aux exigences établies.
Si nous distinguons le composant qui forme le plus souvent la base de l'argile, il s'agit alors de la kaolinite - l'un des silicates d'aluminium hydratés. En outre, la composition des matières premières utilisées peut inclure de la montmorillonite, de l'illite, du quartz et d'autres ingrédients mineurs.
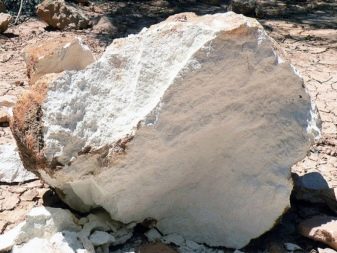
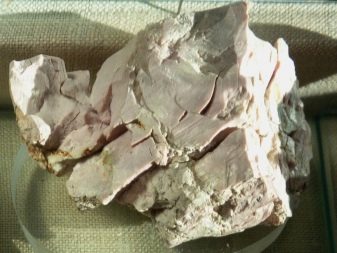
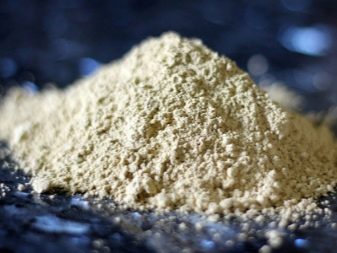
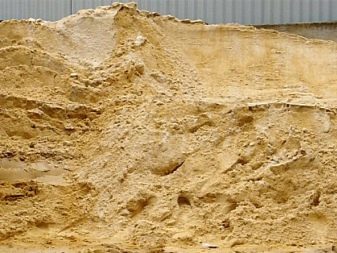
En plus de l'argile, les briques en céramique sont composées d'autres composants qui sont des additifs. Ils sont utilisés pour conférer certaines propriétés aux produits manufacturés, et les principaux sont les suivants.
- Émacié - cendres, sable, scories. Favorise une meilleure formation de masse et moins de retrait.
- Burnout - sciure de bois, charbon en poudre ou tourbe. Ils augmentent la porosité du matériau, ce qui réduit naturellement sa densité.
- Coloration - en règle générale, les oxydes métalliques. Ils donnent aux produits la couleur ou la nuance désirée.
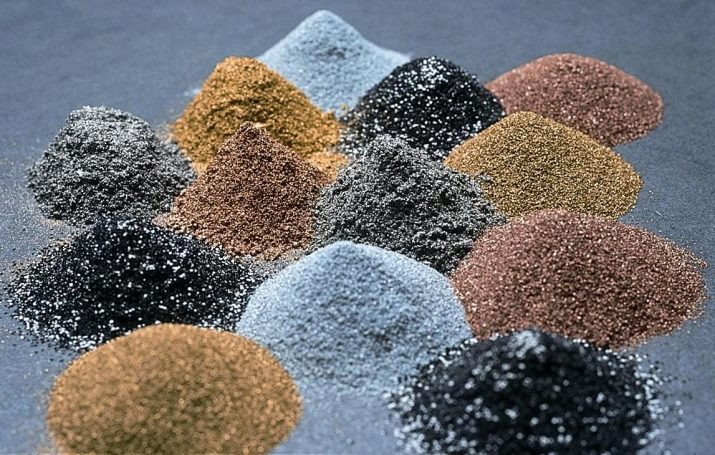
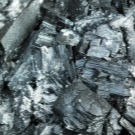
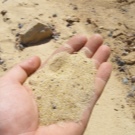
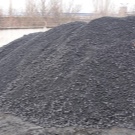
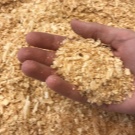
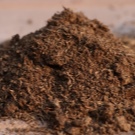
En outre, il convient de mentionner les minerais ferreux et le grès, dont l'utilisation vous permet de contrôler efficacement la température de cuisson.
En outre, des plastifiants peuvent être utilisés - des additifs qui minimisent le risque de fissuration du matériau céramique.La quantité spécifique de chacun des ingrédients énumérés est déterminée par les exigences du client et/ou la politique du fabricant.
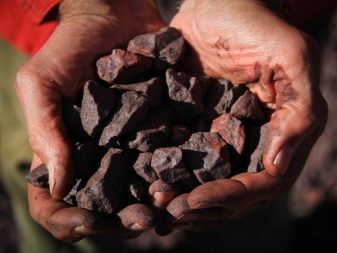
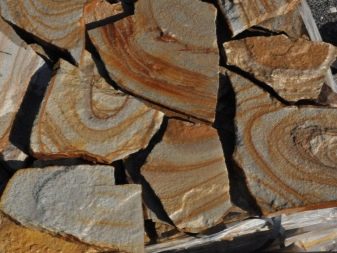
Silicate
La production de briques blanches implique l'utilisation de trois composants obligatoires, dont la liste est la suivante.
- Sable... Il peut être d'origine naturelle ou artificielle. Il est souhaitable que les grains utilisés soient homogènes et aient une taille de 0,1 à 5 mm. Les caractéristiques de surface des grains de sable sont non moins importantes (en présence d'angles vifs, ils offrent une meilleure adhérence). Une condition préalable est le nettoyage préalable du matériau des inclusions étrangères.
La proportion recommandée de sable dans les briques de silicate est de 85 à 90 %.
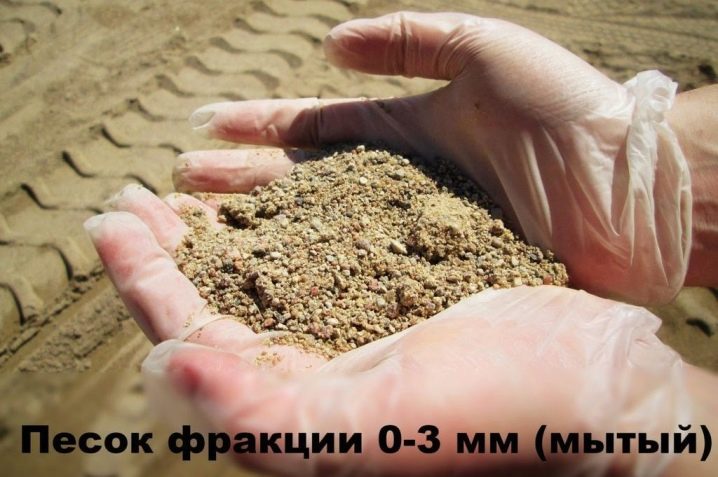
- Chaux... Pour obtenir ce composant, des matières premières sont utilisées, qui se distinguent par une teneur élevée en carbonate de calcium (90 % ou plus) - tout d'abord, du calcaire et de la craie. Avant la cuisson à une température d'environ 1150 ° C, la roche préparée est broyée à une taille ne dépassant pas 10 cm.À la fin des procédures énumérées, de la chaux est ajoutée à la composition des briques de silicate (la valeur optimale est de 7%).
- L'eau... Cet ingrédient est nécessaire pour résoudre deux tâches principales - éteindre la chaux et conférer de la plasticité à la masse en formation. Il est utilisé à toutes les étapes de la fabrication des briques de silicate.
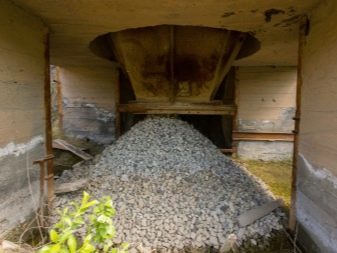
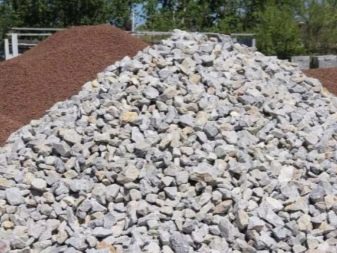
Souvent, la production des produits décrits implique l'utilisation de composants supplémentaires nécessaires pour conférer au produit les caractéristiques souhaitées.
- Composants chimiques... Un exemple est le dioxyde de titane, grâce auquel les briques de silicate restent blanches aussi longtemps que possible.
- Composants qui augmentent la résistance au gel... Le plus souvent, pour résoudre ce problème, on utilise des produits de traitement industriel qui permettent de réduire de 10 à 12% la conductivité thermique du matériau.
- Teintures... Ils sont utilisés dans des situations où un fabricant doit donner aux produits une nuance ou un ton spécifique.
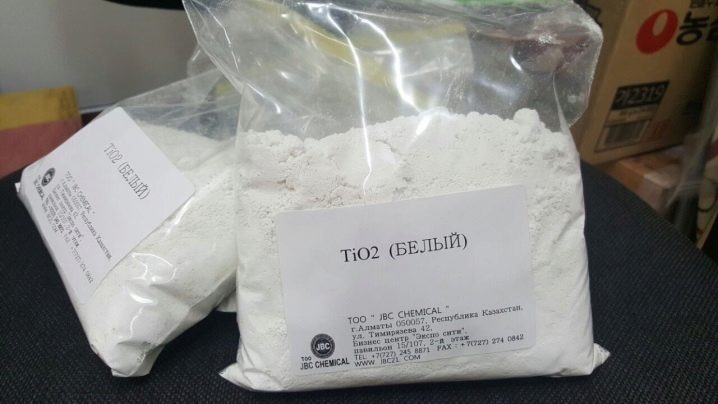
Le sable argileux expansé mérite également d'être mentionné - un additif capable de résoudre simultanément deux problèmes à la fois. En plus d'une augmentation notable de l'efficacité thermique des produits silicatés, cela leur donne une belle couleur café, grâce à laquelle ils ont un aspect plus solide.
Technologie de production
Selon le type de briques produites, leur production a ses propres caractéristiques. Cela est dû à la spécificité des ingrédients utilisés, ce qui nécessite l'utilisation de divers procédés technologiques.
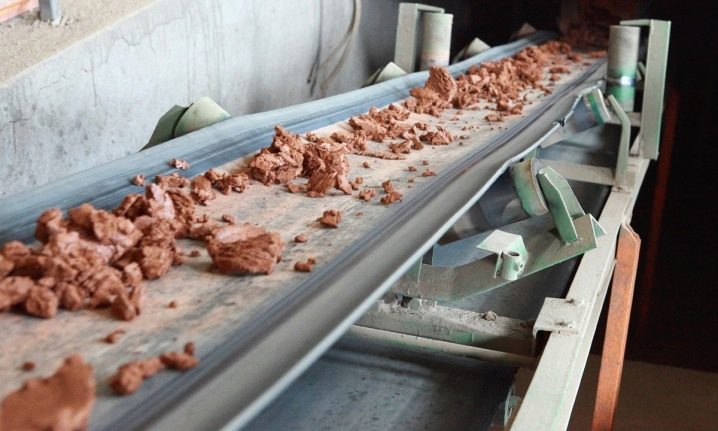
rouge
Il existe deux méthodes principales pour la production de briques en céramique - le moulage semi-sec et le plastique. Ce dernier, qui est plus populaire, implique la résolution étape par étape des tâches suivantes.
- Préparation du composant principal - argile. Il est permis d'inclure des additifs dans le mélange - pas plus de 1/3 de son montant total. Dans ce cas, la fraction de l'ingrédient principal ne doit pas dépasser 1,2 mm.
- Transfert de la masse préparée pour un moulage ultérieur.
- Diviser un tableau commun en types.
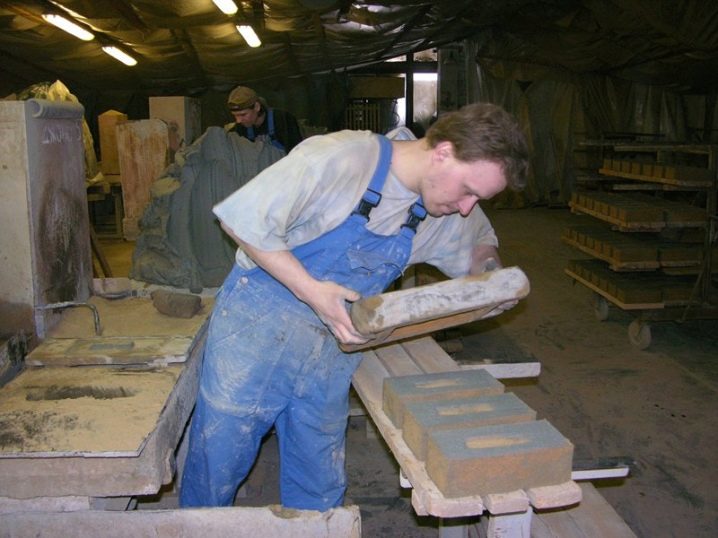
- Séchage de briques en céramique.
- Perforation des produits (pertinente dans les situations où les produits doivent être creux).
- Brûlant. Ce type de traitement permet un changement en douceur de la température dans le four (d'abord vers le haut, puis vice versa). Suivre cette règle vous permet d'éviter l'apparition de fissures sur les briques dues à des changements brusques de température.
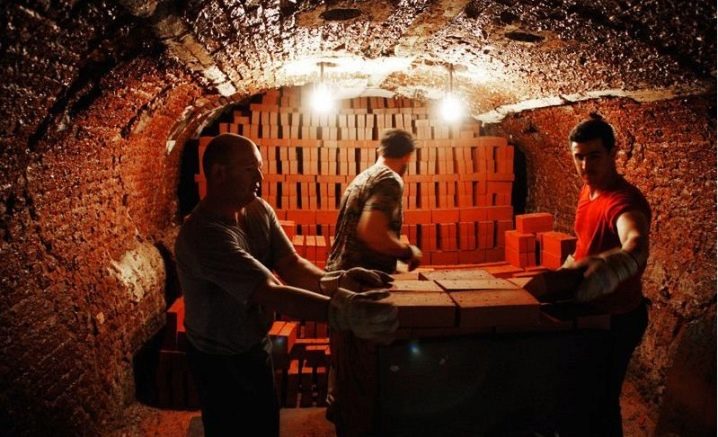
Quant à la production de briques en céramique par la méthode de moulage semi-sec, elle implique la procédure suivante :
- préparation des matières premières et leur broyage;
- séchage et rebroyage;
- légère humidification à la vapeur ;
- re-séchage;
- élimination des dernières traces d'humidité des produits céramiques.
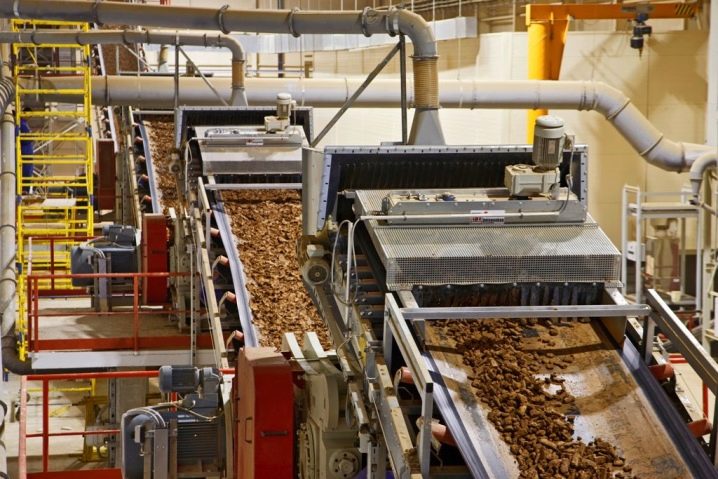
Il est raisonnable de mentionner la production de brique rouge à la maison: de cette manière, il est tout à fait possible de fabriquer une variété "brute" corsée de ce matériau.
Pour résoudre un tel problème, il faut :
- faire une boule à partir d'un morceau d'argile homogène, préalablement humidifié avec de l'eau;
- inspectez soigneusement l'échantillon après 4 jours - pour la présence de retrait inégal et de fissures;
- s'il n'y a pas de défauts visibles, la balle doit être lâchée au sol ;
- si l'échantillon ne passe pas le test de résistance, sa composition doit être renforcée avec des additifs appropriés.
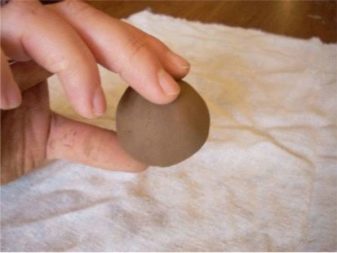
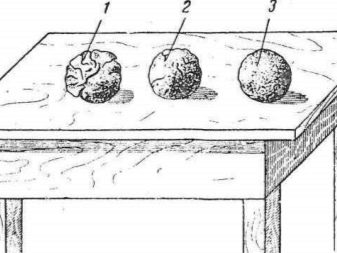
Une fois toutes les procédures préparatoires terminées, le mélange doit être réparti sur les coffrages en bois. Les produits céramiques finis seront laissés à sécher à l'ombre, après quoi ils pourront être utilisés pour la construction de bâtiments légers à un étage.
Pour rendre les surfaces plus durables, il est conseillé de les recouvrir de peinture ou de mortier de ciment de haute qualité.
blanche
L'une des principales caractéristiques de la fabrication de briques silico-calcaires est la complexité, qui ne permet pas de résoudre ce problème à la maison. En particulier, cela s'explique par une liste impressionnante d'équipements nécessaires - convoyeurs et convoyeurs, concasseurs et doseurs, mélangeurs et autoclaves, grues et chargeurs.
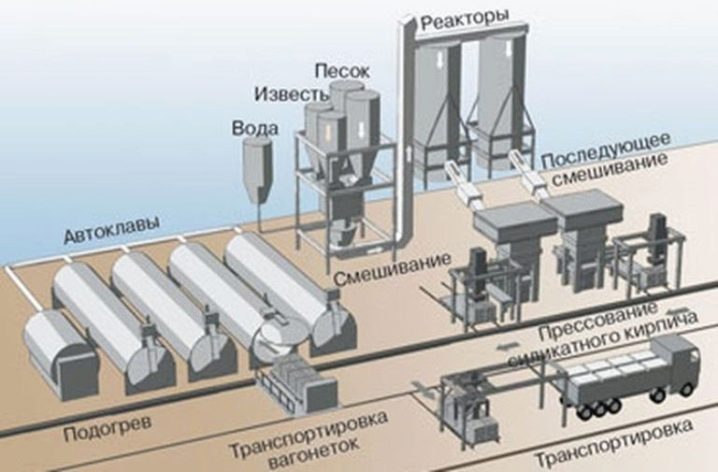
Il existe deux principales méthodes de production pour les produits considérés - le tambour et le silo.
La technologie de fabrication de briques de silicate comprend les étapes suivantes :
- vérifier et préparer les principaux composants - sable et chaux (le premier est séparé des grosses inclusions et le second est broyé);
- mélange des composants suivi d'une décantation dans le bunker ;
- broyer le mélange et y ajouter de l'eau;
- extinction de la chaux, réalisée en fût ou en silo (déterminé par le mode de production choisi) ;
- éliminer l'humidité du sable;
- moulage avec une presse;
- traitement à la vapeur en autoclave (température recommandée - 180-190 ° C, pression - 10 atmosphères).
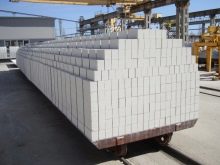
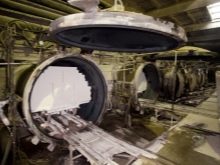
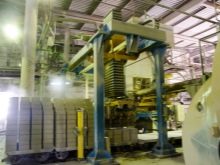
Au stade final, la température et la pression sont progressivement réduites. Une fois toutes les procédures stipulées par la technologie terminées, les briques silico-calcaires prêtes à l'emploi sont emballées et envoyées au client.
Types de tir
Le processus de traitement thermique des briques en céramique, appelé cuisson, mérite une considération distincte. Il représente l'étape finale de la production de ces produits et prévoit la présence de 3 étapes - le chauffage, la cuisson elle-même et le refroidissement.
- Les briques sont chauffées à 120°C pour en éliminer l'eau restante.
- Pour éliminer les inclusions d'origine organique et les dernières traces d'humidité, la température est portée à 600°C, puis à 950°C, ce qui confère aux produits une résistance supplémentaire.
- À la fin du durcissement, les briques sont refroidies, abaissant progressivement la température.
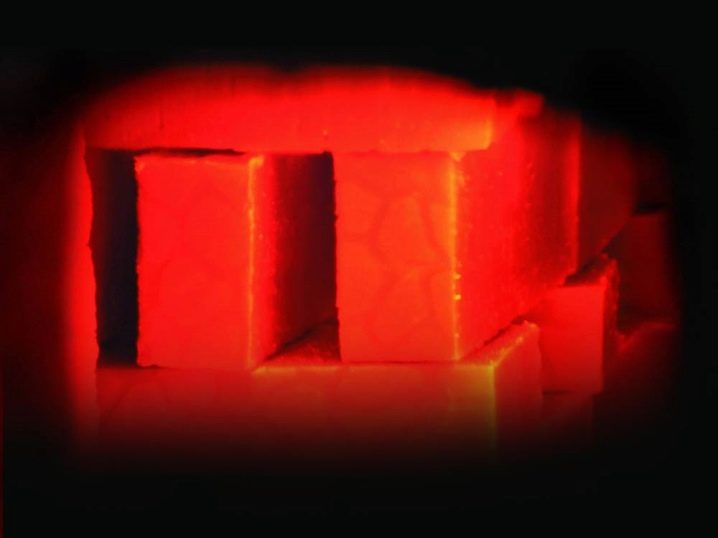
Si la technologie est suivie, un produit avec une structure uniforme et une teinte rouge orangé sera obtenu.
Je voudrais également mentionner deux types d'appareils utilisés pour résoudre le problème décrit ci-dessus.
- Tunnel... Il s'agit d'un long four étanche, composé de 3 chambres, à l'intérieur desquelles sont posés des rails pour le transport des briques en céramique. Dans la première chambre, les produits sont séchés, dans la seconde - cuisson à l'aide de brûleurs et dans la troisième - refroidissement.
- Annulaire... La conception de ce four suppose la présence d'un grand nombre de sections distinctes, qui ont leur propre source de chaleur et sont placées sous la forme d'un anneau. Sa particularité est que les briques passent par toutes les étapes de cuisson sans quitter les limites d'une chambre. Ainsi, le compartiment adjacent fournit un chauffage initial, la calcination est effectuée grâce à sa propre source de chaleur et le refroidissement du produit se produit sous l'influence de la section suivante.
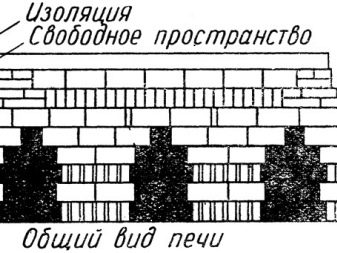
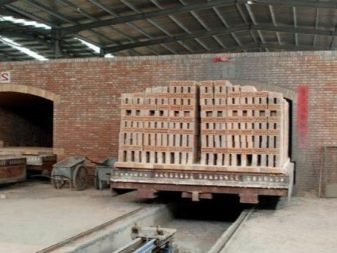
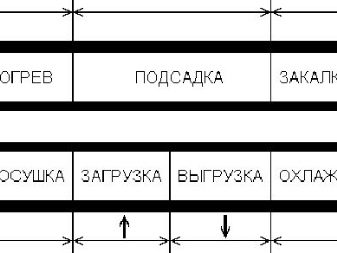
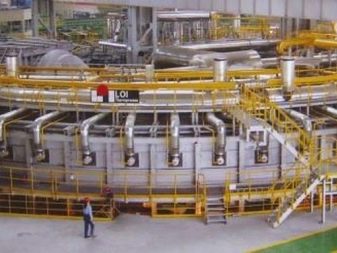
Ainsi, la connaissance de la technologie de production de briques vous permet d'obtenir un matériau solide, esthétique et résistant à l'usure à partir de matières premières fragiles et pliables, qui n'ont initialement aucune valeur pour le constructeur.
Les subtilités de la production de briques modernes sont décrites en détail dans la vidéo ci-dessous.
Le commentaire a été envoyé avec succès.