Un aperçu du polyuréthane pour la fabrication de moules

Pour la production de divers produits, par exemple de la pierre non naturelle, des matrices sont nécessaires, c'est-à-dire des moules pour verser la composition durcissable. Ils sont principalement en polyuréthane ou en silicone. Vous pouvez facilement créer de telles formes de vos propres mains.

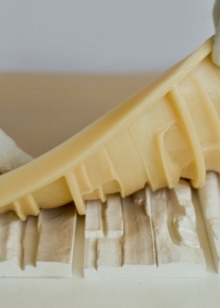

Particularités
La pierre est de plus en plus souvent utilisée dans la conception d'espaces de bureaux et de logements. Le prix élevé d'un produit naturel et sa popularité ont donné une impulsion à la production d'imitation. La pierre artificielle de bonne qualité n'est pas inférieure à la pierre naturelle, ni en beauté ni en résistance.
- L'utilisation de polyuréthane pour la fabrication de moules est la solution la plus réussie et en même temps la plus économique.
- Le moule en polyuréthane permet de retirer facilement le carreau durci sans casser et conserver sa texture. En raison de la plasticité de ce matériau, le temps et les coûts de production de la pierre décorative sont économisés.
- Le polyuréthane permet de transmettre avec une précision maximale toutes les caractéristiques du relief de la pierre, les plus petites fissures et la surface graphique. Cette similitude rend aussi difficile que possible de distinguer visuellement une pierre artificielle d'une pierre naturelle.
- Des matrices de cette qualité permettent d'utiliser des matières premières combinées pour la production de carreaux décoratifs - plâtre, ciment ou béton.
- La forme du polyuréthane se caractérise par une résistance, une élasticité et une durabilité accrues, résiste avec succès aux effets de l'environnement extérieur. Les moules tolèrent parfaitement le contact avec la surface abrasive.
- Les formes de ce matériau sont fabriquées dans une variété d'options, ce qui vous permet de créer un large assortiment de pierre artificielle avec une empreinte prononcée d'une surface naturelle, des briques décoratives avec une répétition absolue des effets visuels du matériau vieilli
- Le polyuréthane est capable de modifier ses paramètres en fonction de la charge, du colorant et d'autres additifs. Vous pouvez créer un matériau capable de remplacer le caoutchouc dans ses paramètres - il aura la même ductilité et la même flexibilité. Il existe des espèces qui peuvent reprendre leur forme initiale après déformation mécanique.
Le composé de polyuréthane se compose de deux types de mortiers. Chaque composant a un type différent de base de polyuréthane.
Le mélange des deux composés permet d'obtenir une masse fluide homogène qui se solidifie à température ambiante. Ce sont ces propriétés qui permettent d'utiliser le polyuréthane pour la fabrication de matrices.
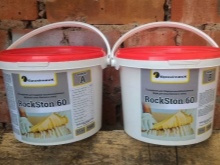


Vues
Le polyuréthane moulé est une matière première à deux composants de deux types :
- coulée à chaud;
- coulée réfrigérée.
Parmi les marques à deux composants sur le marché, on distingue particulièrement les suivantes :
- porramolds et vulkolands;
- adiprène et vulcoprène.

Les fabricants nationaux proposent les qualités SKU-PFL-100, NITs-PU 5, etc. Dans leurs technologies, ils utilisent des polyesters de fabrication russe qui ne sont pas de qualité inférieure aux analogues étrangers, mais les surpassent à certains égards. Le polyuréthane à deux composants nécessite certains additifs pour modifier la qualité des matières premières. Par exemple, les modificateurs accélèrent la réaction, les pigments modifient le spectre de couleurs, les charges aident à réduire le pourcentage de plastique, ce qui réduit le coût d'obtention du produit fini.
Utilisé comme charge :
- talc ou craie;
- du noir de carbone ou des fibres de différentes qualités.


La méthode la plus courante consiste à utiliser la méthode de coulée réfrigérée.Cela ne nécessite pas de compétences professionnelles particulières ni d'équipement coûteux. L'ensemble du processus technologique peut être appliqué à la maison ou dans une petite entreprise. La coulée à froid est utilisée dans la production de produits finis prêts à l'emploi et pour la décoration des joints et des surfaces.
Pour la coulée à froid, on utilise du polyuréthane moulé par injection, qui est un type liquide de plastique durci à froid.... La méthode de coulée à ciel ouvert est utilisée pour la réalisation de pièces techniques et d'éléments décoratifs.
Le formoplast et le silicone peuvent être considérés comme des analogues du polyuréthane moulé par injection.

Timbres
Le polyuréthane liquide est utilisé dans la fabrication de matrices à diverses fins, le choix d'un composé en dépend.
- Pour obtenir des formulaires matriciels de petite taille - savon, moules décoratifs, petites figurines - Le composé "Advaform" 10, "Advaform" 20 a été créé.



- Dans le cas de la fabrication de moules pour couler des mélanges de polymères, un autre type est utilisé, par exemple l'ADV KhP 40. Le polymère a été développé dans ce but précis - il peut devenir la base d'autres types de compositions polymères. Il est utilisé dans la coulée de produits en silicone et en plastique. Ce composant a la capacité unique de résister activement aux influences agressives.


- S'il est nécessaire de réaliser de grandes formes pour des produits massifs tels que des sculptures, des blocs de construction, des ornements architecturaux de grande taille, utilisez la pâte à couler à froid "Advaform" 70 et "Advaform" 80... Ces qualités forment une substance de haute résistance et dureté.


Composants pour la fabrication
Pour obtenir une forme en polyuréthane, vous devez disposer de tous les composants du processus technologique :
- composé de moulage par injection à deux composants;
- pierre naturelle ou son imitation de haute qualité;
- matériau pour la boîte de cadre - aggloméré, MDF, contreplaqué;
- tournevis, vis, spatule, capacité en litres;
- mélangeur et balances de cuisine;
- diviseur et silicone sanitaire.

Méthode de préparation.
- Les carreaux de pierre sont disposés sur une feuille de MDF ou de contreplaqué, installée strictement horizontalement. Un espace de 1-1,5 cm est laissé entre chaque carreau, les bords du moule et la partie centrale de division doivent être plus épais, au moins 3 cm.Après avoir choisi l'emplacement le plus approprié pour les prototypes, chaque carreau doit être collé à la base en utilisant du silicone.
- Après cela, il est nécessaire de faire le coffrage. Sa hauteur doit être supérieure de plusieurs centimètres à celle du carreau de pierre. Le coffrage est fixé à la base avec des vis autotaraudeuses et les joints sont scellés avec du silicone pour éviter les fuites de polyuréthane liquide. La surface est exposée et vérifiée avec un niveau. Une fois le silicone durci, une lubrification est nécessaire - toutes les surfaces sont recouvertes de l'intérieur d'un séparateur, après cristallisation, il forme le film le plus fin.
- Le polyuréthane moulé par injection à deux composants est mélangé dans des proportions égales, pesant chaque composant. Le mélange résultant est soigneusement amené à une masse homogène avec un mélangeur dans un récipient préalablement préparé et versé dans le coffrage. La technologie nécessite un traitement sous vide, mais à la maison, peu de gens peuvent se le permettre, alors les artisans se sont adaptés pour s'en passer. De plus, la surface de la pierre a un relief complexe, et une petite diffusion de bulles restera invisible.
- Il est plus correct de verser la masse résultante dans le coin du coffrage - lorsqu'elle s'étendra, elle remplira de manière dense tous les vides et expulsera simultanément l'air. Après cela, le polyuréthane est laissé pendant une journée, au cours de laquelle la masse durcit et se transforme en une forme finie. Ensuite, le coffrage est démonté, si nécessaire, coupé avec un couteau en polyuréthane ou en silicone et séparez le coffrage du prototype. Les carreaux bien collés doivent rester à la surface du support. Si cela ne s'est pas produit et que la tuile est restée en forme, il est nécessaire de la presser, peut-être de la couper soigneusement.
La forme finie a le temps de sécher, car elle sera légèrement humide à l'intérieur - elle doit être essuyée et laissée pendant quelques heures. Le moule est alors prêt à l'emploi.

Critères de choix
Lors du choix du polyuréthane de moulage, il faut se rappeler : la température maximale qu'il peut supporter est de 110 C. Il est utilisé pour les résines et les métaux à bas point de fusion. Mais sa solidité et sa résistance à l'abrasion le rendent indispensable pour travailler le gypse, le ciment, le béton, l'albâtre. Tous ces matériaux ne donnent pas une température supérieure à 80 C pendant le processus de durcissement :
- pour le moulage en plâtre afin d'obtenir une pierre artificielle, on utilise du polyuréthane chargé de la marque "Advaform" 300;
- lorsque vous travaillez avec du béton pour des dalles de pavage, des briques, la marque la plus appropriée est "Advaform" 40;
- pour obtenir des ornements décoratifs, un composé de la marque Advaform a été développé pour les panneaux 3D 50 ;
- "Advaform" 70 et "Advaform" 80 sont utilisés pour le moulage d'objets de grande taille.
Si vous considérez attentivement le but de chaque marque, il ne sera pas difficile de choisir le type de polyuréthane moulé par injection requis, ainsi que d'obtenir par la suite des produits finis de haute qualité.
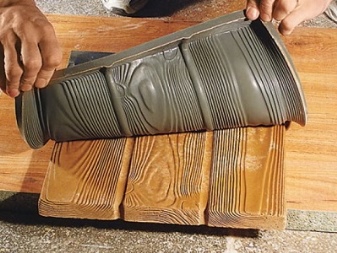

Pour plus d'informations sur la fabrication d'un moule en polyuréthane de vos propres mains, voir la vidéo suivante.
Le commentaire a été envoyé avec succès.